Most people associate chainsaws with cutting down trees, pruning branches and clearing brush, but that is not the kind of chainsaw this post will be covering. Instead, we will be taking a look at chainsaws that have been specially designed to cut concrete, rock and stone. These chainsaws look very similar to the tools homeowners grab to take care of landscaping chores, but they have a couple of key differences. They use water instead of oil to provide lubrication and cooling, and they have far tougher chains.
Concrete Chainsaws
Tradespeople refer to these heavy-duty tools as concrete chainsaws, but they are used to cut metal and stone as well as concrete. Concrete chainsaws are almost always powered by gasoline, but a few electric models have been introduced in recent years. They look very similar to standard chainsaws at first glance, but a closer inspection reveals several important differences. Instead of an opening to add oil, these chainsaws have a connection on the back that is used to attach a water hose. Cutting through concrete or stone causes a lot of vibration, so these chainsaws usually have ergonomic handles and advanced damping systems. While these differences are all important, what really sets concrete chainsaws apart is their diamond chains.
Diamond Tip Chainsaw Chains
Making a chainsaw that can cut through wood is fairly straightforward. Wood is a fibrous and relatively soft substance, so a chain made out of stainless steel can cut through a log or branch with ease. Cutting through tougher materials like stone requires a far tougher chain. Blades or chains must be harder than the substances they cut, so a concrete chainsaw must have a cutting edge harder than stone. Scientists use the Mors scale to give substances a hardness rating of between one and 10, and diamond has the highest rating of all.
The First Diamond Saws
The first diamond saw blade was introduced in 1926. The Felker diamond segmented blade was coated in diamond grit that had been embedded in metal segments. The blade was created by welding these segments to a steel core. The Felker blade was a large tool that was designed to be used in factories rather than on jobsites, and it was prohibitively expensive.
Diamond blades remained confined to large manufacturing facilities for the next 10 years, but that all changed in 1936 when the Clipper Electric Masonry Saw was unveiled. This tool used abrasive carborundum and diamond segmented blades to cut through concrete and stone, and it was small and light enough to be used on construction sites. This was a paradigm shift as cutting stone had been done with hammers and chisels up to that point.
For several decades, diamond blades were circular and fitted to cut-off saws, but this approach has several drawbacks. Over-cutting is a common problem, and a circular blade with a 14-inch diameter has a maximum cut depth of just five inches. Chainsaws cut deeper and with more precision, so it was only a matter of time before diamond chains for chainsaws began to appear.
Modern Diamond Saws
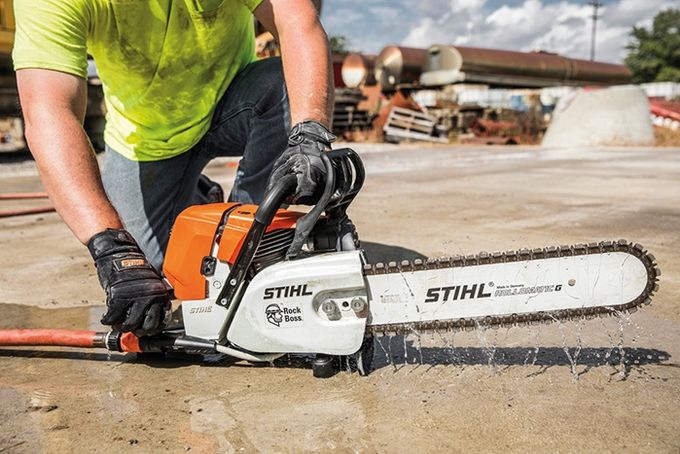
The latest concrete chainsaws still get their cutting power from diamonds, but the stones are now made in a lab instead of being dug out of the ground. Laboratory diamonds have the same physical and chemical properties as natural diamonds, but the heat and pressure that creates them is provided by machines rather than the forces of nature. Instead of embedding diamond grit in metal that is then welded into place, modern diamond chainsaw blades are made using a sintering process. This is done by mixing diamond grit with metal powder and then sintering the mixture onto the chain. Using synthetic rather than natural diamonds has lowered the price of diamond chainsaw chains, but they are still a lot more expensive than stainless steel chains.
How Are Concrete Chainsaws Used?
Concrete chainsaws are designed to cut through concrete, stone and even metal, but they don’t cut in the traditional sense. Instead, their diamond chains use a grinding action to wear away tough materials like brick and rock, which is why you would not use a diamond tip chainsaw chain for wood. Grinding takes a little longer than cutting, but it is much safer. Stainless steel chainsaw blades can kick back dangerously when they snag on wood, but the grinding action of a concrete chainsaw eliminates kickback.
Concrete chainsaws are also used differently. When cutting a log, the bottom of the chainsaw blade is placed against the material. When cutting concrete or stone, the tip of the chainsaw blade is pushed into the material. This is possible because there is no kickback, and it makes concrete chainsaws extremely versatile. They can perform complex cuts that would be impossible with other power tools, and they can even be used to make holes in walls.
Diamond blades for chainsaws are usually found on construction sites being used to cut concrete, pipes and asphalt, but they have many other uses. Sculptors use them at the beginning of projects to remove large sections of stone, and fire departments use them to gain access to burning buildings. Concrete chainsaws are also used to clear rock obstructions in mines.
- Exclusive Chain For Wall Cutting Machines:This Chain Is Exclusive For Wall Cutting Machine, Please Note The Model Number When Purchasing.
- Powerful cutting ability: easily cuts walls, reinforced concrete, rock and other materials.
- Durable Quality: Built with high quality materials, After High Temperature Quenching, The Chainsaw Chain Is High Temperature Resistant, Good Wear Resistant, Not Easy To Be Elongated, Continuous Cutting.
- Please Notes: Please Confirm Your Parameters To Ensure This Chain Suit Your Machine Before Buying. Not All Bars Take The Same Amount Of Links.
- Any problem, we would like to provide suggestions.
The Importance of Water
Concrete chainsaws are usually run at full throttle, so they generate enormous amounts of heat and dust when they cut through hard materials like stone. To deal with these problems, concrete chainsaws have connections that allow them to be hooked up to water supplies. Pumping water along the blade keeps temperatures down, and it also protects workers from dangerous airborne particles.
The clouds of dust that appear when stone is cut are made out of tiny silica particles that can penetrate deep inside the lungs and have been linked to serious diseases including cancer. Spraying the cutting surface with water prevents these clouds from forming. To prevent overheating and maintain workplace safety, concrete chainsaws should be connected to a reliable water supply with at least 20 psi of pressure and a flow rate of no less than four liters per minute.
Concrete chainsaws also use their water supplies to clean and lubricate their nose sprockets. This is usually done by running water through channels on the guide bar. The scum that builds up in water tanks and the dust that is created when concrete and stone are cut can foul nose sprockets, so water should be run through a concrete chainsaw for several seconds after cutting has been completed. This flushes out nose sprockets and removes any sludge.
Chain Tension and Guide Bars

The chain tension should be checked every time a concrete chainsaw is used. The chain should be just loose enough to allow it to be pulled around the guide bar without too much difficulty. If the chain is too tight, the chain will not last as long, and the nose and drive sprockets will wear prematurely. If the chain is too loose, it could slip over the drive sprocket and damage the drive links.
Concrete chainsaws have guide bars that can be turned over, which means that both sides can be used. To prevent uneven wear, guide bars should be flipped periodically. Doing this can be compared to rotating the tires on an automobile. You will know that a guide bar has reached the end of its service life when both sides are so worn that the drive links bottom out.
Cutting With a Concrete Chainsaw
Concrete chainsaws are usually operated at full throttle, but only the appropriate amount of force should be used. Chainsaws can lug or stall if too much force is used, and they could skip over materials instead of cutting them if operators are too gentle. If a new diamond chain is being used, its diamonds should be “opened up” before work commences. This is done by making a few small cuts in an abrasive material like brick or cinder block. Before making any cuts, operators should check all safety devices and clear any obstructions from the cutting surface. They should also wear a helmet with a face shield, hearing protection, gloves and toes with steel toecaps.
Before connecting a concrete chainsaw to a water supply and switching it on, a marker pen should be used to make an outline of the intended cut. The saw should then be warmed up by holding the trigger at full throttle for several seconds. Once the saw is ready to use, the nose of the guide bar should be pushed about a half inch into the material. This is called a plunge cut. The rest of the outline should then be followed until the entire cut has been scored. Once this has been done, the entire cut can be deepened to about two inches.
After the initial scoring has been completed, the final cut can commence. This is done by plunging the chainsaw through the material until it reaches the opposite side. Plunge cuts should be made around the entire outline until the piece of material being cut away can be removed. Plunge cuts reduce chatter, lengthen chain life and save time, but burying the nose of the guide bar for prolonged periods can lead to chain stretching. This is because buried chains do not clear debris as effectively, which can cause slurry to accumulate at the tip. If making straight cuts is difficult, the guide bar is likely worn and needs to be turned over. It should be remembered that guide bars are only meant to provide a track for the chain, and they should never be used to pry, twist or lift the material being cut.
Cutting Rebar
A different approach should be taken when steel reinforcing rods are encountered. Plunge cuts are not appropriate in these situations as rebar is ductile and stretches, so a rocking motion should be used instead. Rocking the saw keeps the diamond tips exposed to improve cutting, and it allows operators to cut rebar and concrete simultaneously. Most concrete chainsaws have a wall walker fulcrum to make this easier. This is an assembly near the handle of the saw that features a lever, arm, wedge and spring. When the fulcrum is pushed against a wall, the handle of the saw can be moved up and down. This provides a four to one mechanical advantage, which makes cutting rebar much easier. However, using a concrete chainsaw to cut metal will shorten chain life significantly even if its wall walker feature is used.
Making Deep Cuts in Concrete and Stone
Being able to make deep cuts is one of the main advantages of using a concrete chainsaw. Circular saw blades make shallow cuts, but chainsaws can bury their entire guide bars into material. This means they can cut through up to 16 inches of concrete. Using a concrete chainsaw becomes difficult when cuts go beyond six inches as vibration becomes more severe, but many saws have sophisticated damping systems to minimize this problem.
Diamond Cut Chain Vs Regular Chainsaws
Chainsaws may all look alike, but they don’t all work alike. Regular saws have stainless steel chains that are perfect form cutting wood, but concrete chainsaws are designed to cut through tougher materials and have chains tipped with diamonds. While both types of saw use basically the same technology, they are not interchangeable. A stainless steel chain lacks the harness to cut rock or stone, and using a diamond chain to cut wood will result in rough and crooked cuts. Regular and concrete chainsaws are designed for specific applications, so choosing the right tool for the job should not be a challenge.
- Sturdy material: made of quality emery grain, which has good polishing effect, uniform and delicate carving, hard texture, the material is rust and wear resistant, sturdy and lightweight, not easy to break, deform or bend
- Wide range of applications: widely applied in grinding and engraving workpieces, such as jade, ceramics, glass, cemented carbide and gemstones, there may be some black spots on the surface of sharpening wheels, it is the coating is off, but a normal phenomenon in transportation, this does affect the use
- Multiple specifications: there are 3 specifications and sizes, the length is 1.8 inches, which are suitable for saw blade wheels such as 5/32 inch electric saws, 3/16 inch small oil chain saw wheels, 7/32 inch large oil chain saw wheels, different sizes are convenient for you to use and replace in your daily life
- Easy to install: the chain saw sharpener is easy to install and can be replaced in 2 steps; You can apply polishing without removing the chain, which saves you time and effort and improves work efficiency
- Sufficient quantity: you will get 30 pieces of hardness diamond chain saw sharpeners in 3 different sizes, which are convenient to carry and store, enough for you to apply in daily life and meet your replacement needs
- High-Speed & Fast Sharpening--Without removing the chain, the chain saw sharpener can do the sharpening job in just a few minutes.A great replacement for a hand chain saw file/ sharpener.
- Great Sharpening Effect--The emery particles are evenly distributed on the surface, so you can get a fine and uniform filing effect, making the chain as sharp as ever. Get no saw powder, just big flakes.
- Reusable --Made of titanium-coated emery, chain saw shaperener tool are solid, strong and not easy to break. Much longer life than other grinding wheels without titanium plating.
- 21Pcs Chain Saw Blade Shaperener Set--3 sizes grinding head diameter:5/32''(4.0 mm), 3/16''(4.8 mm), 7/32''(5.5 mm).Each size is 7Pcs; Shank diameter:3 mm , Total length:1.77''. Different size meet your diverse needs.
- Wide Application--Perfect for grinding chainsaw. Widely applied in mechanical and metal, wood, jade, glass polishing. Such as molds, steel bars, etc.A practical gift for dad husbands and lumber jacks.
- Sturdy and durable material: made of quality emery grain, which has good polishing effect, uniform and delicate carving, hard texture, the material is rust and wear resistant, sturdy and lightweight, not easy to break, deform or bend.
- 3 Sizes: 5/32'' wheels for Electric chainsaw and other small blade, 3/16'' wheels for small oil chainsaw, 7/32'' wheels for large oil chainsaw.
- Easy to Install: The chain saw sharpener is easy to install, It can be changed in just two steps. Besides, this titanium-coated file is harder and more wear-resistant, so you don’t have to change it often.
- Wide Application: These Diamond Chainsaw Sharpeners are widely used in machinery, bearings, metal polishing, chain saws, molds, jade, wood, solder joints, weld grinding, burr grinding, etc.
- Package include: 3 Size Diamond Chainsaw Sharpener Stones with storage box, each size with 12pcs(10pcs gold and 2pcs siliver).